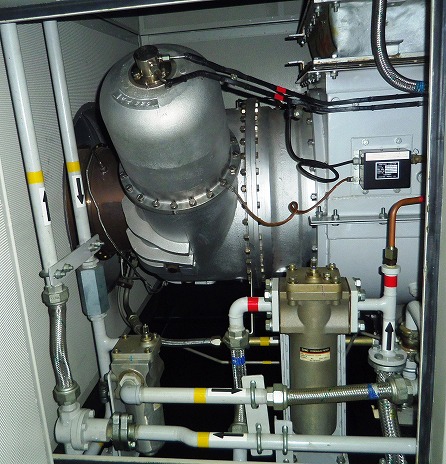
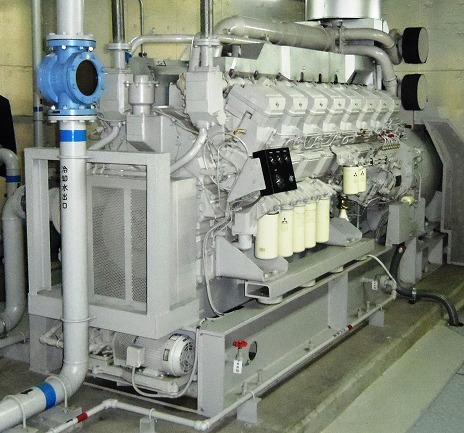
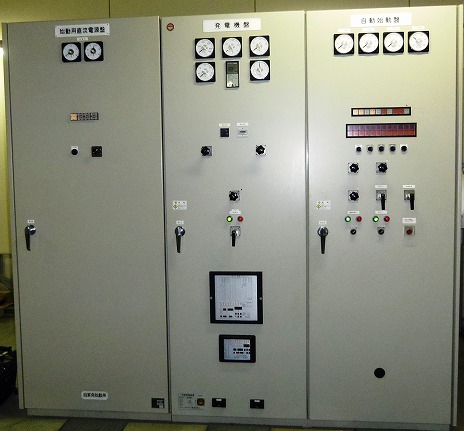
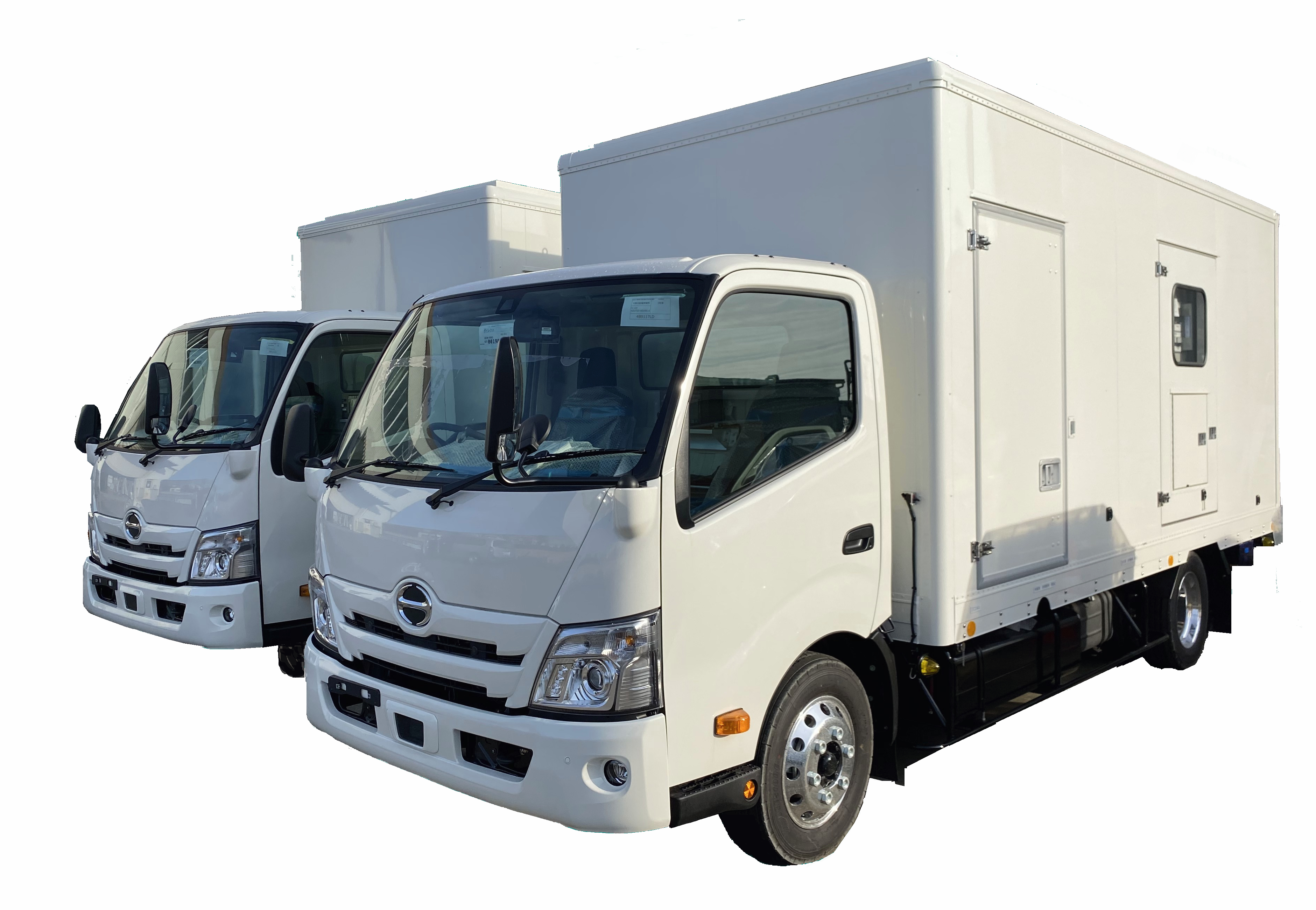
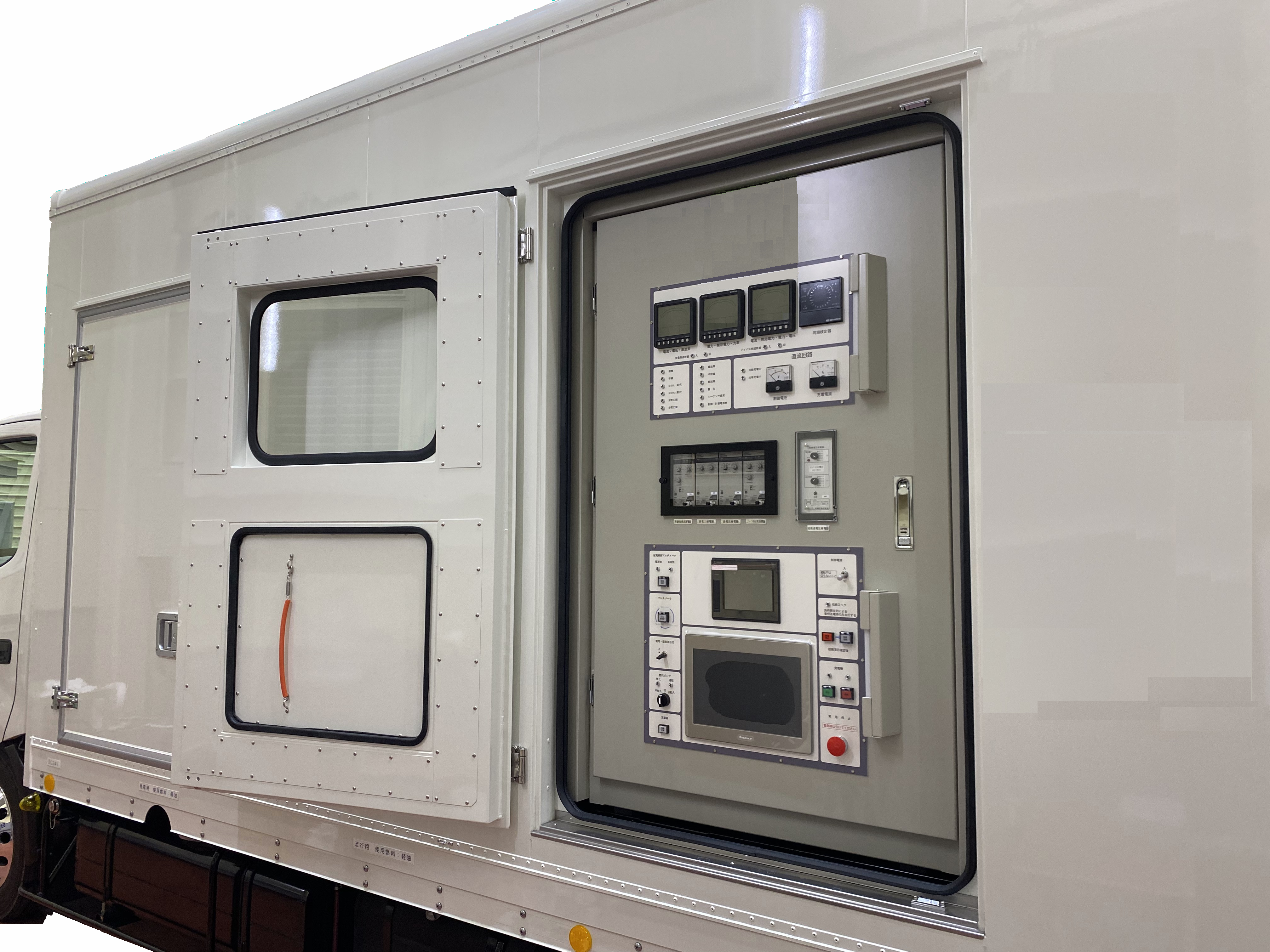
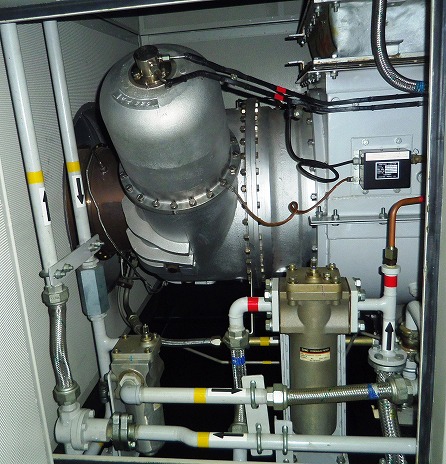
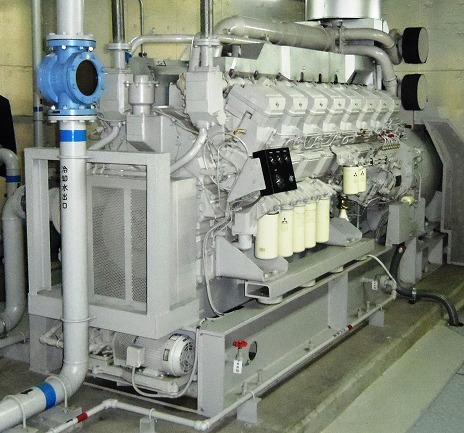
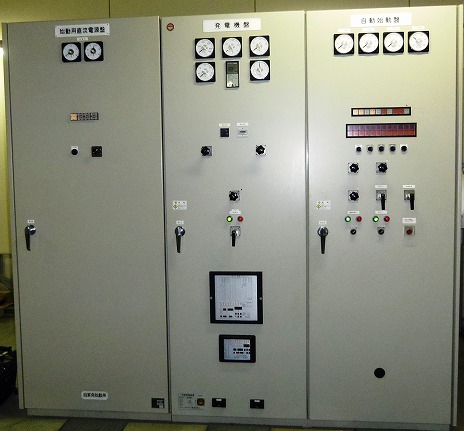
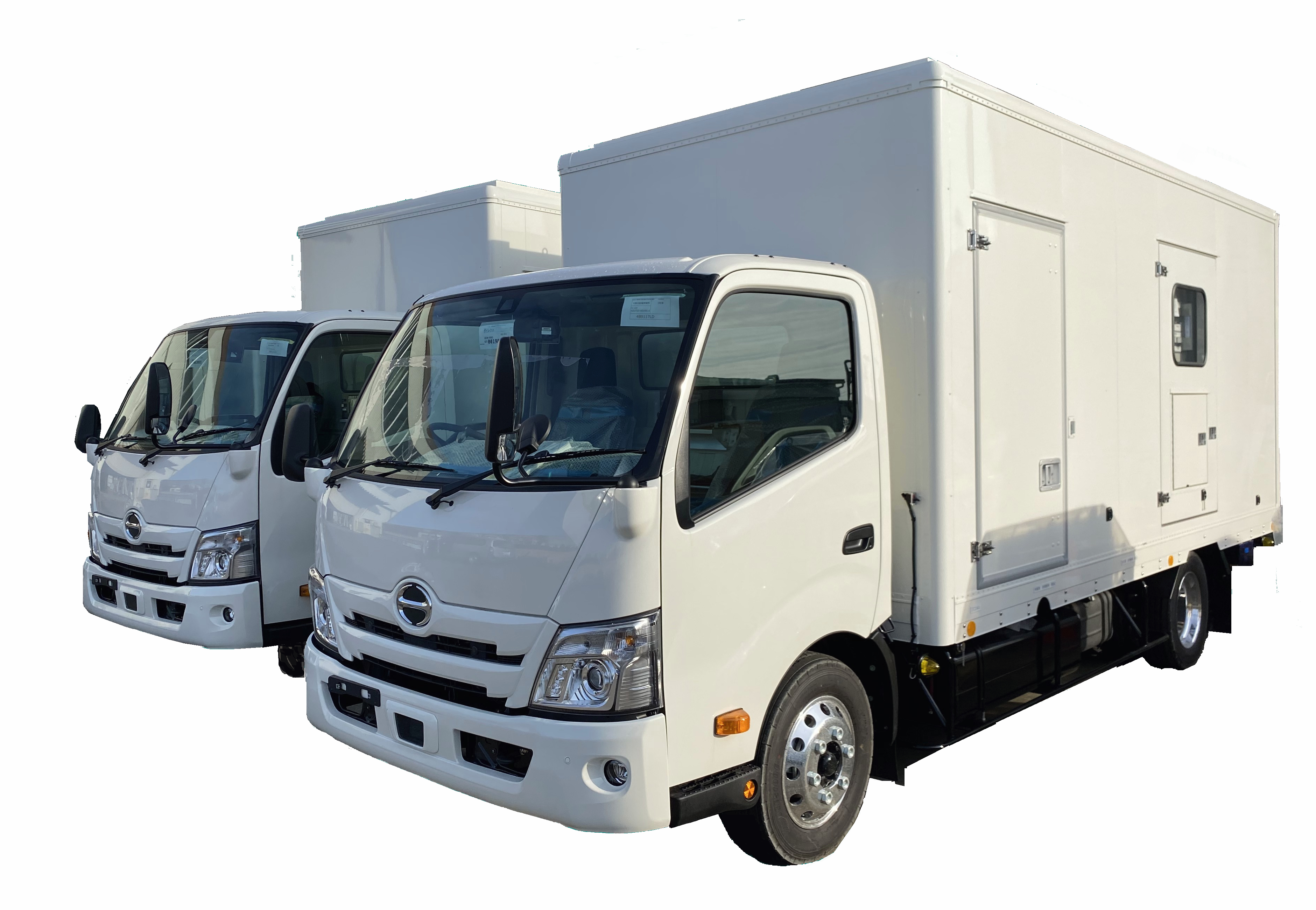
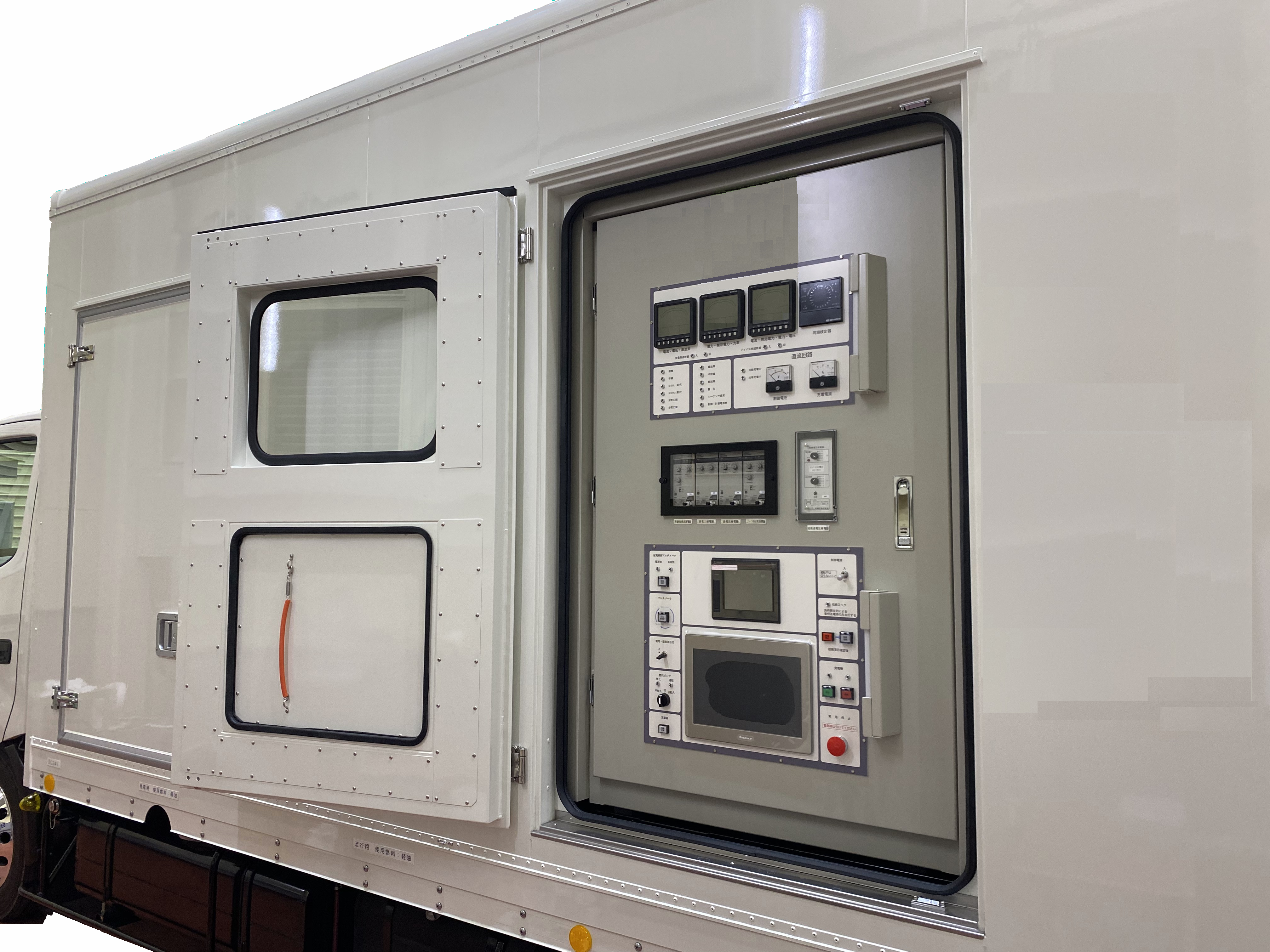
Power Generation Facilities
Our engineers are experienced in the technologies of private power generation facilities and power generation control systems. We dispatch these engineers to perform periodic inspections, parts replacement, repairs, modifications, and improvements according to manufacturers' standards. As a group of maintenance professionals, we also offer consulting proposals adapted to the customer's facility environment. The Meiden Customer Center (MCC) provides 24-hour telephone support to give customers confidence through corrective maintenance.
Features
- The manufacturer's engineers, who have expertise in the facilities and equipment, formulate appropriate inspection cycles and parts replacement schedules, and work on preventive maintenance based on accumulated data.
- To ensure that customers can use facilities with peace of mind, we dispatch our technicians and promise high quality maintenance.
- Power generation facilities that constitute an emergency power supply adapted to fire-fighting equipment, etc., are subject to various regulations such as the Fire Service Act and the Building Standards Act. Our qualified expert engineers perform inspections of these facilities.
- We can assist with customer Business Continuity Plans (BCP).
Malfunction Case Studies
- Are inspections of your power generation facility limited to statutory 6-month and annual inspections?
- Do you have equipment that has not been inspected or serviced in 5 years or more?
If left unattended, an emergency power generating system will not work even though the facility has lost power, or it may work, but only for a few minutes.
In the event of a power outage due to a natural disaster or equipment accident, the emergency power generating system must deliver electricity reliably. Such systems play an important role in helping people evacuate safely and quickly.
Some causes of malfunctions are as below.
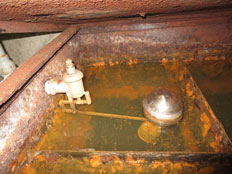
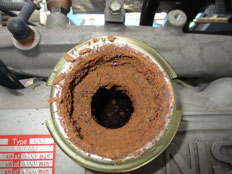
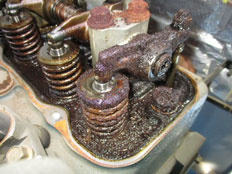
Maintenance and Inspection Services
In order to prevent accidents and malfunctions, we offer maintenance and inspection services based on the inspection cycle below, taking into consideration the customer's requirements and the condition of the equipment.
Inspection Cycle
- 01Inspections of power generation facility in accordance with the Fire Service Act
- ①Equipment inspection (once every 6 months)
- ②Comprehensive inspection (once every 12 months)
- ③Load operation (simulated load of 30% or more: one year or six years)★1
- ④Preventive maintenance measures (replacement of parts in accordance with the manufacturer's recommended replacement schedule)
★1:If ④ preventive maintenance measures are implemented in inspection , the next load operation can be extended to 6 years.
- 02Diesel engines
- ①Two-year inspection
- ②Four-year inspection
- ③Inspection (overhaul) every eight years
- 03Gas turbine engine
- ①three-year maintenance
- ②Six-year maintenance
- ③Twelve-year maintenance
- ④Eighteen-year maintenance (engine replacement)
- 04Hydroelectric power generation facilities electrical component detailed inspection (every 5 to 10 years)
- 05Inspection of fuel service tanks, low pressure water tanks, underground water tanks, and other ancillary facilities (once a year)
- 06Underground tanks, exhaust mufflers, and other ancillary equipment (after 10 years)
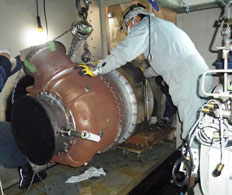
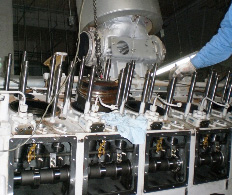
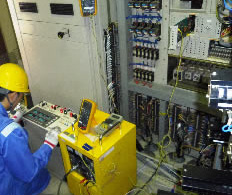
Equipment diagnosis
Even if there is no problem with the exterior, there can be an abnormality inside the equipment.
We use diagnostic tools to carry out diagnoses on the internal unseen areas.
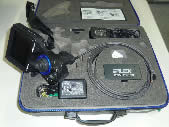
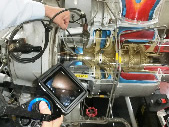
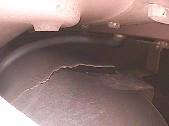
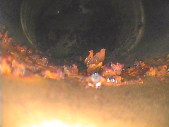
Equipment diagnosis
We renew equipment in response to malfunctions and facility problems caused by equipment whose performance has deteriorated due to long-term use or aging.
Renewal of gas turbine exhaust duct
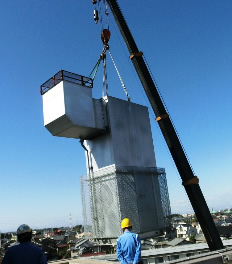
AVR Renewal
We can replace a discontinued product with a successor model or, as preventive maintenance, a control panel with the same functions as the existing panel by using new parts.
AVR are available in a variety of types, depending on the application.


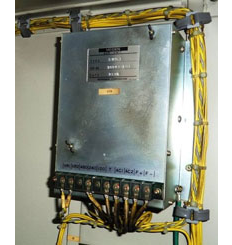
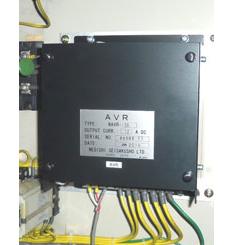
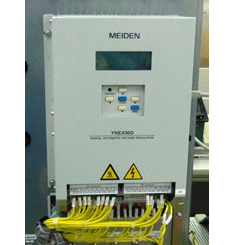